What Is Stamping?
Stamping is a cold stamping processing method that relies on the power of standard or special stamping equipment to hit materials to cut, bend or shape them into the finished shape and size specified by the mold. Stamping processing can be roughly divided into several different processing types such as shearing, bending, forming and extension. The machine tool used for stamping is called a punch machine, and the mold used is called a stamping die. Stamping is usually done on a cold sheet of metal, and forging shapes the hot metal.
Advantages of Stamping
Accurate
Accuracy and consistency are critical to maintaining expectations while delivering quality to consumers. Stamping provides an efficient, accurate manufacturing process to deliver precise parts for a variety of uses, including medical devices and automotive parts.
High cost performance
Once the mold is established, automation means the stamping process becomes more cost-effective than other metal processing and manufacturing techniques. And stamping can still form complex parts quickly and accurately.
Speed
Stamping machines can produce parts at a high rate of speed, making it an ideal process for high-volume production runs. Unlike other manufacturing processes, such as welding or machining, stamping does not require extensive set-up time and can be repeated with consistent quality.
Durability
They are usually made from high-quality metals or alloys, which give them their strength and resilience. Stamping also provides a uniform material thickness and smooth edges, reducing the likelihood of weak spots or fractures.
Automated production
Automated production refers to the use of machines and other automated systems to perform various processes and tasks in a manufacturing environment. The stamping process, which involves the use of a press to cut and shape metal or other materials, is one area of production that can be automated for increased productivity and efficiency.
-
12
3
Why Choose Us
Corporate Culture
Quality-oriented, scientific and technological innovation, scientific management, excellent products, and a good reputation—we wholeheartedly provide customers with the most satisfactory service.
Human Resources
Our existing engineering and technical staff account for 55% of our workforce. The professional management team, assisted by the company's ERP system, serves customers scientifically and efficiently in accordance with the ISO9001 system.
Our Team
We have more than 10 technical engineers, 6 drawing engineers, 8 quality inspection engineers, and 12 professional domestic and foreign sales engineers.
Our Markets
Our products are sold both domestically and internationally, particularly in North America and Europe. For example, we have customers in the United States, Canada, Germany, Switzerland, France, Italy, the Netherlands, Belgium, Poland, Spain, Ukraine, and more.
Types of Stamping
Blanking
This type of stamping involves cutting a flat piece of metal into a desired shape, such as a circle, rectangle, square, or other geometric shape. Blanking is usually the first step in the stamping process and is used to create a high volume of identical parts quickly and efficiently.
Piercing
Piercing is a stamping technique that involves cutting out a hole or opening in a metal workpiece. The process is similar to blanking, but instead of cutting out a shape, a hole is created in the metal.
Bending
Bending is a stamping technique used to create curves or angles in a metal workpiece. The metal is placed in a press and then bent into the desired shape using a die or stamp.
Drawing
Drawing is a stamping technique used to create a cylinder, cone, or other curved shape. The metal is pulled through a die or stamp, which stretches and shapes the metal into the desired shape.
Embossing
Embossing is a stamping technique used to create a raised or sunken design on the surface of a metal workpiece. The metal is pressed into a die or stamp that has the desired design, creating a three-dimensional effect.
Coining
Coining is similar to embossing, but it is used to create a more precise and durable design. The metal is pressed into a die or stamp that has a highly detailed design, creating a crisp and precise image on the metal.
Automotive industry
Stamping is extensively used in the automotive industry to manufacture various auto parts such as body panels, brackets, gears, shafts, suspension components, and many more. Stamping helps to produce these parts in large quantities at a lower cost.
Aerospace industry
The aerospace industry uses stamping technology to produce precision parts such as flight control components, brackets, and airframe structures. Stamping helps to create lightweight, strong, and durable parts that can withstand harsh environments.
Electronics industry
Stamping is used in the electronics industry to create various electronic components such as connectors, shields, and cases. The stamped parts have high conductivity and provide electromagnetic shielding, which makes them perfect for electronic applications.
Medical industry
Stamping is used in the medical industry to produce surgical instruments, implantable devices, and medical equipment. The stamped parts are biocompatible and can withstand harsh sterilization processes, making them ideal for medical applications.
Consumer goods industry
Stamping is used in the consumer goods industry to manufacture various products such as kitchen appliances, hardware equipment, toys, and jewelry. The stamped parts have a smooth surface finish and can be produced in various colors and textures.
Process of Stamping
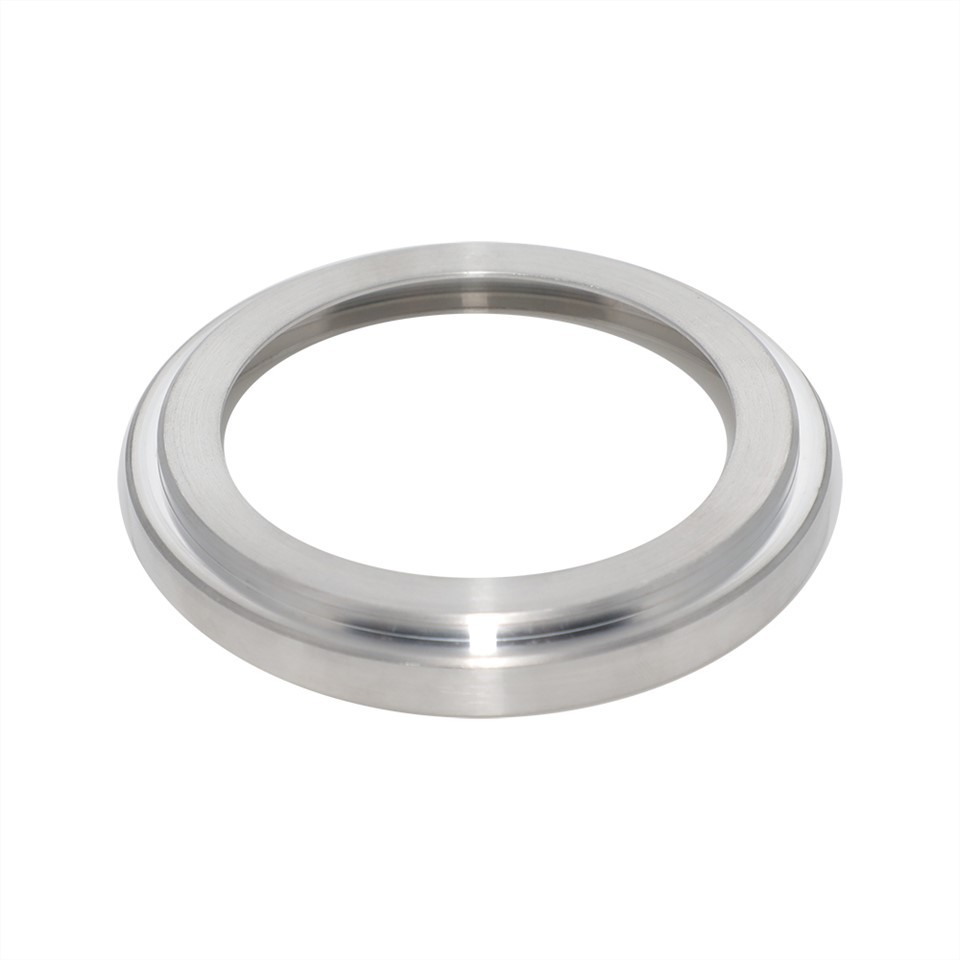
01.Design and tooling
02.Material preparation
03.Stamp setup
04.Stamping
05.Finishing
Components of Stamping
The stamping press is the core component of the stamping process. It is a machine that applies pressure and force to a metal sheet to shape and form it into different shapes and sizes.
A die is a tool that is used to cut or shape the metal sheet in a specific way. It is usually made of hardened steel and designed to produce the desired shape of the finished product.
A punch is a tool that is used to apply force to the metal sheet, which is then shaped by the die. The punch is designed to produce the desired shape and features of the finished product.
A blankholder is a component that holds the metal sheet in place while it is being shaped by the stamping press. It prevents the metal sheet from lifting or moving during the stamping process and helps ensure the accuracy and consistency of the finished product.
Lubrication is crucial in the stamping process, as it helps reduce friction between the metal sheet and the die. This ensures smooth and efficient stamping and helps prevent damage to the die.
The feed system is responsible for moving the metal sheet into the stamping press and positioning it in the correct place to be stamped. It ensures the accuracy of the stamping process and helps prevent waste and damage to the material.
The control system of the stamping press is responsible for monitoring and regulating the stamping process. It ensures consistent and accurate stamping, and also monitors the performance of the machine to prevent damage or downtime.
Stamping is a metalworking process that involves cutting and shaping metal sheets into various shapes and designs. The materials used for stamping are commonly metals, such as steel, aluminum, copper, and brass. These metals are chosen because of their ability to withstand the forces and pressure involved in stamping.In addition to these materials, stamping can also be done on non-metallic materials such as cardboard, leather, and plastic. However, these materials require different stamping techniques and equipment compared to metals.The choice of material for stamping depends on various factors, including the required level of durability, strength, and resistance to corrosion. For example, steel is commonly used for stamping applications that require high strength and durability, while aluminum is preferred for applications that require lower weight and better corrosion resistance.
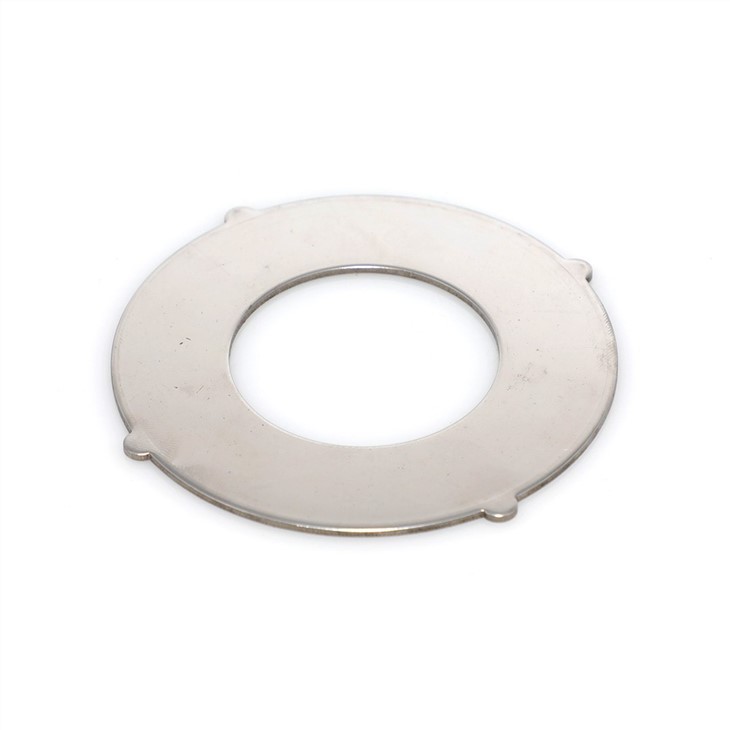
How to Maintain Stamping
Clean the stamped Items regularly
Regardless of the application, stamped items collect dirt, debris, and other contaminants over time. To prevent the accumulation of these particles, it is recommended to clean stamped items regularly. A simple solution of warm water and mild soap can be used to gently clean the surface of the stamped item. Avoid using strong and abrasive cleaning solutions that can damage the surface of the stamping.
Protect the stamped surface
Stamps can wear out over time, especially if they are exposed to harsh weather conditions, chemicals, or abrasive surfaces. To protect the stamped surface, consider applying a protective coat. The type of coating used will depend on the application of the stamped item. For instance, a clear epoxy coating can be used for jewelry making, while a rust protector can be applied to stamped metal parts used in automotive manufacturing.
Store the stamped Items in a safe place
Proper storage is crucial for maintaining the integrity and functionality of stamped items. To prevent damage or degradation, store stamped items in a clean and dry place. Keep them away from direct sunlight, moisture, and extreme temperatures. Additionally, avoid stacking stamped items on top of each other to prevent scratching or rubbing.
Inspect the stamped items regularly
Regular inspection is necessary to identify any damages or deformations that might occur to stamped items. Inspect for any signs of wear, cracks, or rust on the stamped surface. Any defects found should be addressed immediately to prevent further damage or corrosion.
Seek professional help when necessary
If you are unsure about how to maintain a stamped item, it is best to seek professional help. A qualified technician or artisan can provide professional advice on how to maintain various stamped items. They can also offer specialized solutions, such as re-stamping, refinishing, or polishing to restore the stamped surface to its original condition.
What Are the Safety Measures for Stamping Operations
Proper machine guarding
It is essential to ensure that stamping machines are adequately guarded to prevent accidents such as contact with moving parts. This can be achieved by enclosing the machine with barriers and installing interlocking devices to stop the machine when the guard is opened.
Employee training
All employees involved in stamping operations must receive relevant training on the safe use of the equipment, including safety protocols and emergency procedures.
Regular maintenance
Stamping machines require regular maintenance to keep them in good working condition. This includes replacing worn parts and performing routine checks to ensure that the machine is functioning correctly.
Personal protective equipment (PPE)
All employees involved in stamping operations must wear appropriate PPE, such as safety glasses, face shields, hard hats, gloves, and safety shoes.
Good housekeeping
Keeping the work area clean and organized can prevent accidents and reduce the risk of slips, trips, and falls. It is essential to eliminate clutter and debris from the work area.
Emergency procedures
It is essential to have emergency procedures in place for stamping operations. This includes readily accessible first-aid equipment and emergency response plans in case of accidents.
What Factors Should Be Considered When Choosing Stamping
Quality
When selecting a stamping supplier, it is imperative to consider the quality of the products they produce. Ensure that the supplier has a good reputation for producing high-quality products and has a history of producing products that meet industry standards and regulations. You can verify this by asking for testimonials from their previous customers or doing an assessment of their quality control systems and certifications.
Production capacity
The production capacity of the supplier is another important factor to consider. You need a supplier that has the capacity to produce the quantity of stamps you require within the set timelines. Establish the supplier's ability to handle large orders and the turnaround time for new orders.
Delivery time
Delivery time is critical as it will determine the efficiency of your production process. Therefore, ensure that the supplier can deliver within the agreed timeframe. The supplier’s delivery time can be assessed by the duration they take to respond to your inquiries or orders.
Cost
The supplier's price is another factor to consider, but the lowest price is not always the best option. The cost must be evaluated against the quality and timeliness of the product delivery. You should also consider value-add services such as design consultation, logistics support, and customization options.
Materials and equipment
A competent stamping supplier must have the right machinery and equipment for the production process. You should choose a supplier that uses modern and high-quality equipment to ensure that your products are of top quality. Additionally, the supplier must use high-quality materials that meet your specifications.
Reputation
Always consider the supplier’s reputation and the experience they have in the industry. This information can be obtained by researching the supplier's reviews and ratings from other customers, industry associations, and the Better Business Bureau. A reputable supplier may also be able to provide references from previous customers.
Customer service
Excellent customer service can make a significant difference in the efficiency of your production process. The supplier’s ability to provide attentive and responsive customer service, including communication on the status of orders, options for customisation, and technical support, is critical for delivering a seamless experience.

Stamping and engraving are two different methods used to permanently mark or imprint a design, text, or image onto a surface material. Stamping involves the use of metal stamps, which are engraved with the desired text or design, and a hammer or press to stamp the design onto the surface. This method is commonly used on softer materials such as leather, fabrics, and certain metals. The stamped image or text appears raised above the surface of the material, making it a popular choice for adding logos or decorative designs to soft goods. on the other hand, involves the use of a cutting tool to remove material from the surface and create a permanent design or text below the surface level. Engraving is commonly used on harder materials such as metal, glass, and stone. The engraved image or text appears recessed below the surface of the material and can be filled with paint or other materials for added contrast.
How does Stamping work
The material to be stamped is usually cut to the desired size and shape. The material may also be cleaned and prepped to remove any dirt, debris, or contaminants that could interfere with the stamping process.
Stamping tool design
A stamping tool is designed to match the desired shape of the part. The tool is usually made of a hard material, such as steel or titanium, and is shaped like the part that is being stamped.
The stamping tool is placed against the material and pressed down onto it, applying pressure and forcing the material into the desired shape. The tool may be moved back and forth or in a circular motion to create a pattern or design in the material.
After the stamping process, the parts may be finished to remove any rough edges, improve the surface quality, and prepare them for further processing or assembly. This may involve polishing, grinding, or other finishing techniques.
Forming
Stamping is commonly used to form metal sheets or strips into various shapes and configurations. It can create complex geometries, such as curves, bends, flanges, and contours, by applying pressure and force to the metal material. Forming is essential for producing components with specific shapes and dimensions.
Piercing
Piercing is a stamping function that involves creating holes or openings in the metal sheet or strip. It is achieved by using a punch and a die to remove a portion of the material. Piercing is commonly used to create holes for fasteners, ventilation, or other functional requirements in the stamped parts.
Bending
Stamping can also be used to bend metal sheets or strips into specific angles or shapes. This process involves applying force to the material, causing it to deform and take on the desired bend or curve. Bending is crucial for creating components with angled or curved features, such as brackets, clips, or enclosures.
Coining
Coining is a stamping function that involves compressing the metal material between two dies to create intricate details or patterns on the surface. It is commonly used to create embossed or engraved features, such as logos, text, or decorative elements. Coining enhances the aesthetic appeal and functionality of the stamped parts.
Blanking
Blanking is a stamping function that involves cutting out a flat shape from a metal sheet or strip. It is typically used to create flat components or parts that will undergo further processing or assembly. Blanking is often the first step in the stamping process, followed by additional forming or cutting operations.
Assembly
Stamping can also be used for assembly purposes. Multiple stamped parts can be joined together using various techniques, such as welding, riveting, or fastening, to create more complex assemblies or sub-assemblies. Stamping allows for the efficient production of components that can be easily integrated into larger structures or systems.
Cutting
Stamping can be used to cut metal sheets or strips into specific shapes or sizes. This process is often referred to as blanking or shearing. It involves the use of a die and a punch to remove unwanted material from the metal sheet, leaving behind the desired shape. Cutting is crucial for creating precise and accurate parts.