What Is Casting?
Casting is a process in which molten metal, plastic, or other materials are poured into a mold or cavity in order to create a solid object. The process typically starts with a pattern replica of the final product that is placed into a mold, and then molten material is poured into the mold. Once the material has cooled and solidified, the mold is opened, and the cast part is removed. Casting is commonly used in manufacturing and is used to produce a wide range of products, from simple components to complex machinery parts.
Advantages of Casting
Versatility
Casting allows for the production of various shapes and sizes of objects, ranging from small to large and from simple to complicated geometries. This makes it a highly versatile production method suited to a broad range of applications.
Precision
Casting can achieve very high levels of precision, making it an ideal method for creating complex parts with tight tolerances. This precision also makes it possible to produce parts that require minimal machining or finishing, improving cost-effectiveness and reducing lead times.
Cost-effective
Casting can be a cost-effective production method, particularly when producing large quantities of complex parts. This is because it can reduce the number of manufacturing steps required and minimize material waste.
Reduced lead times
Casting can significantly reduce lead times, as once the molds are created, the production process can be automated, allowing for the quick production of large volumes of parts.
Material options
Casting allows for the use of a wide range of materials, including metals, plastics, and ceramics. This makes it ideal for a broad range of applications where different materials are required.
Replication
Casting allows for the replication of complex parts, making it a highly effective method for producing consistent parts in large quantities.
-
22222
2222 -
2222222222222222222
222
Why Choose Us
Corporate Culture
Quality-oriented, scientific and technological innovation, scientific management, excellent products, and a good reputation—we wholeheartedly provide customers with the most satisfactory service.
Human Resources
Our existing engineering and technical staff account for 55% of our workforce. The professional management team, assisted by the company's ERP system, serves customers scientifically and efficiently in accordance with the ISO9001 system.
Our Team
We have more than 10 technical engineers, 6 drawing engineers, 8 quality inspection engineers, and 12 professional domestic and foreign sales engineers.
Our Markets
Our products are sold both domestically and internationally, particularly in North America and Europe. For example, we have customers in the United States, Canada, Germany, Switzerland, France, Italy, the Netherlands, Belgium, Poland, Spain, Ukraine, and more.
Types of Casting
Sand casting
Sand casting is the most popular type of casting. This method involves the use of sand as a mold material. The sand is compacted around a pattern, which is then removed, leaving behind a cavity that can be filled with molten metal.
Investment casting
Also known as lost-wax casting, investment casting is a process that involves creating a pattern made of wax or another material. The pattern is then coated in a ceramic shell, which is heated to remove the wax and create a cavity that can be filled with molten metal.
Die casting
Die casting is a process used to create complex metal shapes by forcing molten metal into a mold cavity under high pressure. The mold is typically made of steel or another durable material and can be reused multiple times.
Centrifugal casting
Centrifugal casting is a technique used to create circular metal parts such as pipes and tubing. In this process, molten metal is poured into a spinning mold, which creates a centrifugal force that pushes the metal towards the edges of the mold, creating a hollow part.
Continuous casting
This process is used to create long metal shapes such as rods and beams. In continuous casting, molten metal is poured into a mold that moves continuously, allowing the metal to cool and solidify as it travels through the mold.
Shell molding
Shell molding is a similar process to sand casting, but instead of using loose sand, a pre-coated sand is used, which forms a more uniform and consistent mold.
Application of Casting
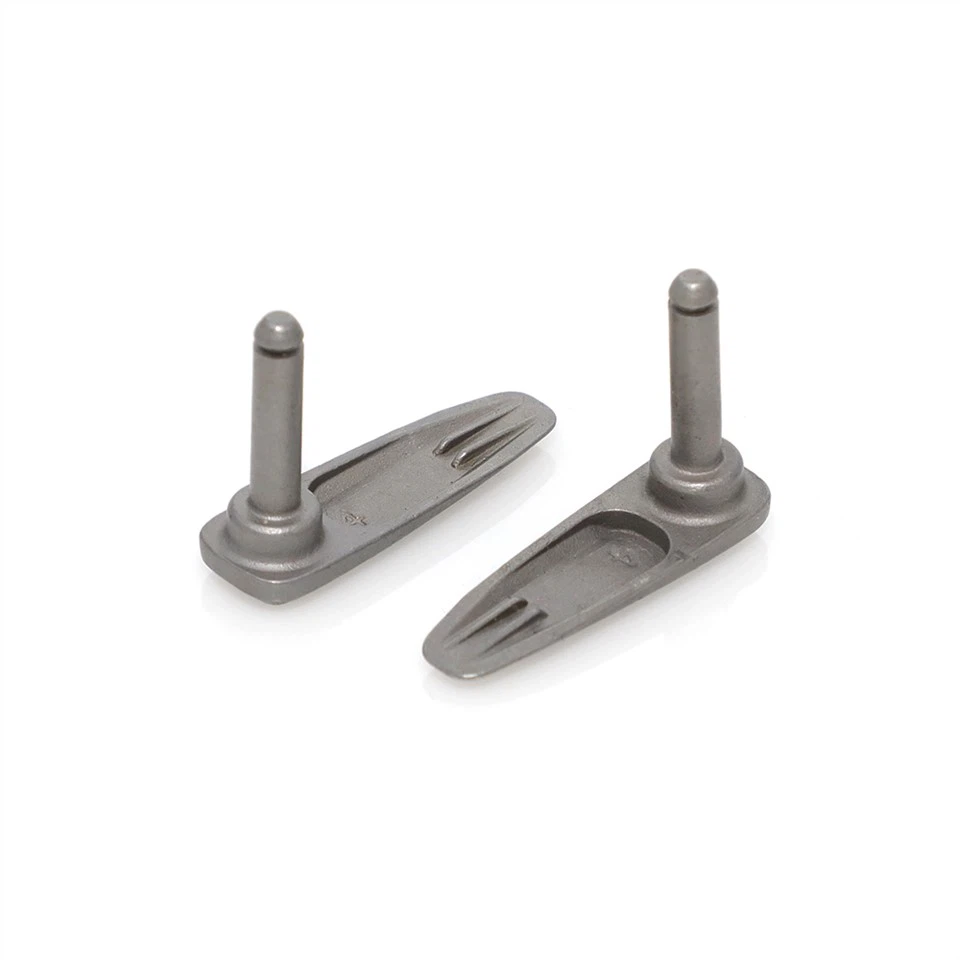
01. Automotive industry
02. Aerospace industry
03. Construction industry
04. Agriculture industry
05. Electronics industry
Process of Casting
Place the mold pattern, which determines the size and shape of the casting, in the sand. The sand (which includes additives) will take the shape of the pattern.
Establish a gating system, consisting of a pouring cup and gates, to direct the molten metal into the mold cavity.
Remove the mold pattern from the sand once the sand has taken its shape.
Pour the molten metal, heated to the appropriate temperature, into the mold cavity through the gating system. The metal can be one of many elements or alloys such as: iron, steel, aluminum, and bronze.
After pouring, the molten metal is left to cool and solidify within the mold. The cooling time varies depending on the type of metal used.
Once the metal has cooled and solidified, open the mold to remove the newly formed metal casting. The mold patterns are typically reusable, but the molds themselves need to be remade for each casting.
What Materials Can Be Used in Casting
Lead alloys
Lead alloys are utilized in certain casting applications, primarily due to their low melting point and malleability. They are used in specialized industries, including: radiation shielding, battery manufacturing, and certain industrial applications. It is important to note that the use of lead is carefully regulated due to its potential environmental and health concerns.
Plastics
Thermoplastics, thermosets, and elastomers can all be used for casting. These materials are melted and poured into a mold and then allowed to cool and solidify. Plastic casting is used in the manufacturing of toys, sports equipment, and medical devices.
Ceramics
Ceramics like pottery, porcelain, and china can be cast using a technique known as slip casting. A liquid clay mixture is poured into a plaster mold and allowed to set until a solid ceramic piece is formed.
Concrete
Concrete can be cast into different shapes and sizes to create a variety of structures including walls, floors, and statues. The process involves mixing cement, sand, and water with an aggregate such as gravel or crushed stone.
Glass
Glass casting involves melting glass and pouring it into a mold. The glass is allowed to cool and solidify before it is removed from the mold. Glass casting is used to create art pieces, decorative objects, and jewelry.
Resin
Resin casting is a process of pouring a liquid resin into a mold, which is then allowed to harden. Resin casting is used in the manufacturing of jewelry, figurines, and other decorative pieces.
Copper alloys
Copper alloys, such as bronze and brass, are popular casting materials known for their excellent electrical conductivity, corrosion resistance, and thermal conductivity. They are commonly used in: electrical and plumbing components, decorative items, and musical instruments.
Steel
Steel is a strong and durable casting material used for applications that require high strength, wear resistance, and impact resistance. It is suitable for heavy-duty components subjected to harsh conditions, such as: machinery parts, construction equipment, and tools.
Yes, casting can definitely be used for mass production. Casting is a manufacturing process where a liquid material is poured into a mold that contains a hollow cavity in the desired shape of the final product. Once the material solidifies, the mold is removed to reveal the finished product.Casting is well-suited for mass production because it is a relatively quick and cost-effective way to create large numbers of identical parts. Once the mold is produced, it can be used to create many copies of the product with minimal additional effort or expense.
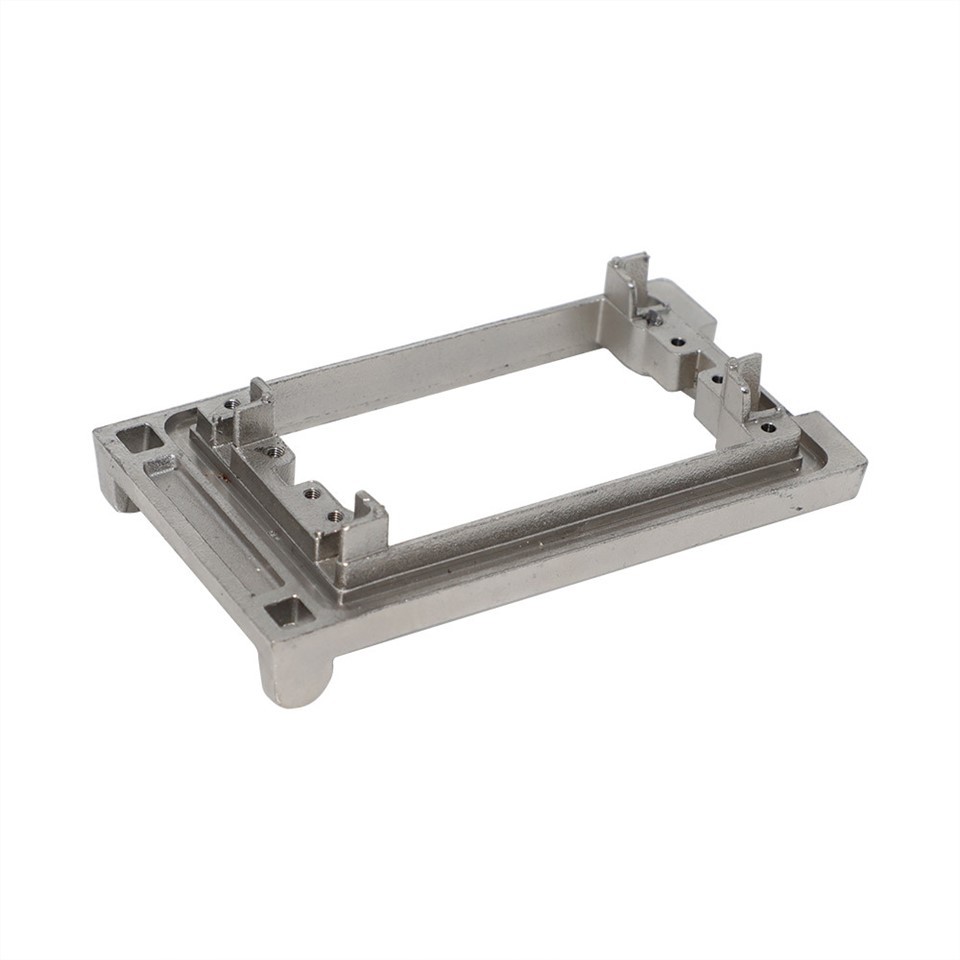
How to Maintain Casting
Regular inspections
Regular inspections of the casting surface will help in identifying any signs of wear and tear. This can also help catch any potential defects early on, before they become a bigger problem or cause damage.
Cleaning
Cleaning the casting regularly helps to maintain its appearance and prevent any build-up of dirt, grease or other materials that can cause issues. A soft-bristled brush or a mild soap and water solution can be used for the cleaning process.
Lubrication
Lubricants are used to reduce friction between moving parts in a casting. Lubrication should be done periodically to ensure that the casting operates smoothly and to prevent damage to the surface.
Storage
Castings should be stored in a dry and well-ventilated area to prevent rust, corrosion or degradation. A coat of rust preventer or oil may be applied to reduce the chances of rusting.
Repairs
If any damages are detected during the inspection, repairs should be carried out as soon as possible to minimize further damage or deterioration. Repairs should be made by a professional who is well-trained and has experience in casting repairs.
Quality control
Regular quality control checks should be conducted to ensure that the casting is functioning as expected. This includes monitoring the casting's dimensional accuracy, surface finish, composition and metallurgical properties.
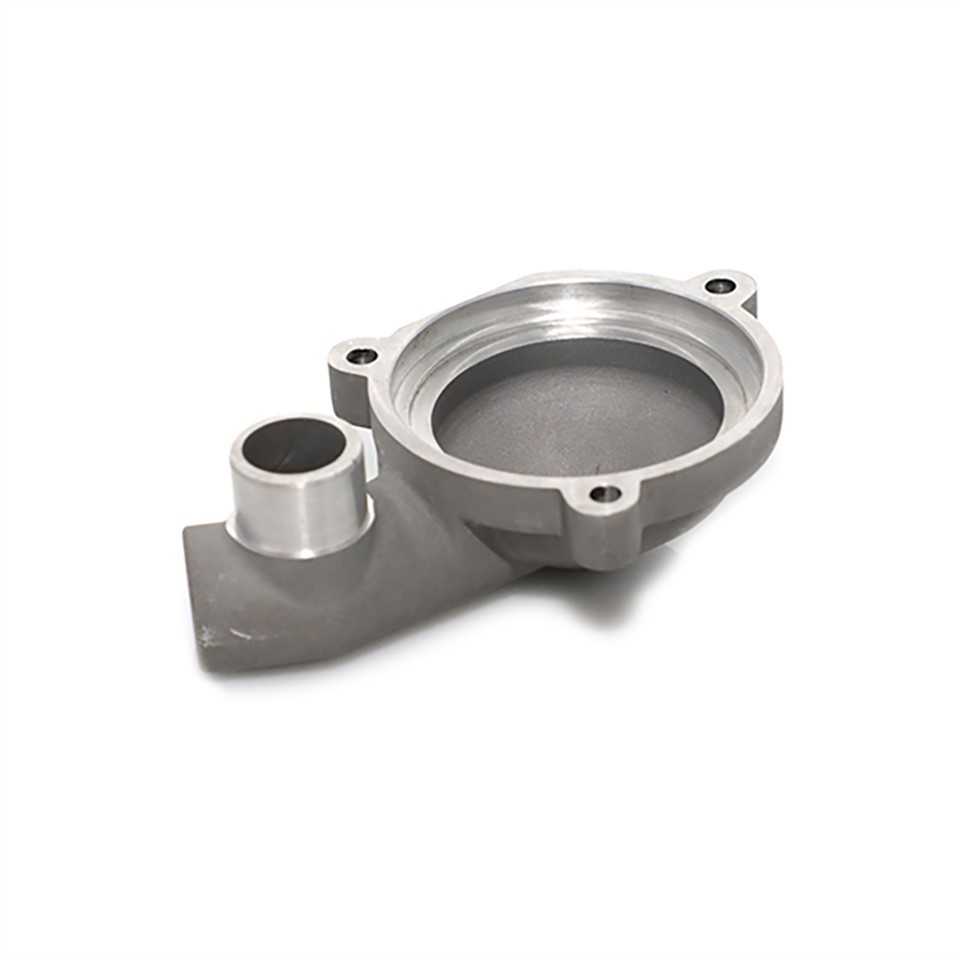
The duration of the casting process can vary greatly and is affected by a variety of factors. The time required for casting depends on: the size of the product, the specific type of casting performed, the size of the sample produced, and the level of labor involved in the process. Therefore, there is no fixed or standard casting time. Timeframes can range from as little as one hour to as long as 2-10 weeks, depending on these variables
How does casting work in manufacturing?
Casting in manufacturing involves the process of pouring molten material into a mold to form the desired shape. The molten material solidifies and forms the shape of the mold, creating the final product. Molds can be made from a variety of materials, such as sand, plaster, or metal, depending on the casting method. After solidification, the casting is removed from the mold, cleaned and further processed as necessary.
How durable are cast products
Cast metal products, especially those that have been heat treated, are very durable. Depending on the metal alloy and application, their service life can range from months to decades. Once the life of the casting is over, the cycle begins again. It is collected in scrapyards, recycled and recast into new items.
Does the thickness of the cast product vary
Yes, the thickness of cast products may vary. The casting process allows the production of parts with varying wall thicknesses, depending on design requirements and the capabilities of the casting method. Different parts of the casting can have different thicknesses to achieve the desired strength, weight and functionality of the final product.
What is the future of casting
The future of the foundry industry holds huge potential through the integration of advanced technologies. Optical measurement systems like the ATOS 3D digitizer are revolutionizing the industry by enabling efficient and accurate measurement of complex surfaces. These systems eliminate the laborious and time-consuming aspects of traditional measurement methods, providing full-field measurements and faster verification. Adoption of such technological advances will improve the productivity, quality control and overall efficiency of the casting process.
Yes, casting is still widely used in various industries. It remains a popular manufacturing process for creating complex metal parts with excellent strength and durability. Casting methods such as sand casting, investment casting and die casting remain vital in sectors such as automotive, aerospace and construction.

How to Operate Casting Equipment Correctly
Preparing the mold
Clean and prepare the mold or pattern that will be used for casting. Ensure that it is free from any debris or contaminants that could affect the quality of the casting.
Melting the metal
If using a furnace, carefully load the appropriate amount of metal into the crucible or furnace chamber. Follow the manufacturer's instructions for the specific type of metal being used and the melting temperature required. Use proper safety equipment, such as heat-resistant gloves and goggles, when handling molten metal.
Preheating the mold
If necessary, preheat the mold to the appropriate temperature to prevent thermal shock when pouring the molten metal. This step is particularly important for certain types of molds, such as ceramic or investment molds.
Pouring the metal
Once the metal is melted and the mold is preheated, carefully pour the molten metal into the mold. Use caution to avoid splashing or spilling the metal, as it can cause burns or other injuries. Follow the recommended pouring technique for the specific type of casting being performed.
Solidification and cooling
Allow the casting to solidify and cool in the mold for the recommended amount of time. This will vary depending on the size and complexity of the casting, as well as the type of metal being used. Avoid disturbing the casting during this process to ensure proper solidification.
Removing the casting
Once the casting has cooled and solidified, carefully remove it from the mold. Use appropriate tools, such as tongs or pliers, to handle the casting and avoid touching it with bare hands, as it may still be hot.
Finishing and cleaning
After removing the casting from the mold, it may require additional finishing and cleaning processes, such as removing excess material, smoothing rough edges, or polishing the surface. Follow the appropriate procedures for the specific type of casting and desired finish.
Equipment maintenance
Regularly inspect and maintain the casting equipment to ensure its proper functioning and safety. Clean and lubricate moving parts, replace worn-out components, and follow any maintenance guidelines provided by the equipment manufacturer.
How to Improve the Performance and Efficiency of Casting
Design optimization
Optimize the design of the casting to minimize the need for complex shapes, thin sections, or excessive material. Simplifying the design can reduce the complexity of the casting process and improve efficiency.
Proper mold design
Ensure that the mold design is suitable for the casting process and material being used. Consider factors such as mold material, gating system design, and venting to optimize the flow of molten metal and reduce defects.
Material selection
Choose the appropriate material for the casting based on the desired properties and application requirements. Consider factors such as strength, corrosion resistance, and thermal conductivity to optimize performance.
Process control
Implement strict process control measures to ensure consistency and repeatability in the casting process. Monitor and control variables such as temperature, pouring speed, and cooling rates to minimize defects and improve efficiency.
Use of simulation Ssoftware
Utilize casting simulation software to analyze and optimize the casting process. This software can help identify potential defects, optimize gating and riser design, and predict solidification patterns, leading to improved performance and efficiency.
Proper heat treatment
Implement appropriate heat treatment processes to enhance the mechanical properties of the casting. Heat treatment can improve strength, hardness, and dimensional stability, resulting in better performance.
Quality control
Implement rigorous quality control measures throughout the casting process. Regularly inspect and test castings for defects, dimensional accuracy, and material properties to ensure high-quality output.
Continuous improvement
Continuously evaluate and analyze the casting process to identify areas for improvement. Encourage feedback from operators and implement changes based on lessons learned to enhance performance and efficiency.
FAQ