What Is Powder Metallurgy?
Powder metallurgy is a processing method that uses metal powder as raw material and makes various products by pressing and sintering. The powder metallurgy process consists of three main steps. First, the main component materials are decomposed into powders composed of many fine particles; then, the powder is loaded into the mold cavity and a certain amount of pressure is applied to form the required part shape and shape. size of the compact; finally, the compact is sintered.
Advantages of Powder Metallurgy
Cost-effective
PM is a more cost-effective manufacturing process compared to traditional methods like casting, forging, and machining. It allows manufacturers to create complex geometries by compacting a pre-measured amount of powder into a precise shape, thereby eliminating the need for cutting and other processing stages.
Precision and consistency
Powder Metallurgy is a precise and consistent process that can produce parts with tight tolerances and minimal machining requirements. This means that manufacturers can create parts to exact specifications without the need for costly post-processing stages.
Material flexibility
Powder Metallurgy offers material flexibility as it can be used on a wide range of materials. This makes it suitable for the production of parts made of various metals, including stainless steel, copper, nickel, and aluminum.
Improved material properties
PM enables manufacturers to create parts with improved material properties like strength, hardness, and wear resistance. This is possible because the powder is compacted under high pressure, resulting in a more homogeneous and dense material.
Reduced waste and environmental impact
Powder Metallurgy generates less waste compared to traditional manufacturing processes like machining and casting. Also, since it doesn't require any cutting fluids or lubricants, it has a smaller environmental footprint.
Increased design flexibility
PM allows for intricate and complex part designs to be achieved through an injection molding process, producing parts that would be difficult or impossible to manufacture through other means.
High production rate
Powder Metallurgy allows for the production of high volumes of parts with consistent quality, making it a suitable process for mass production.
Enhanced surface finish
Powder Metallurgy can produce parts with a refined surface finish, reducing the need for additional finishing operations.
-
12222222222
222222222 -
1哇哇哇哇哇哇哇哇哇哇
哇哇哇哇哇哇哇哇哇哇哇
Why Choose Us
Corporate Culture
Quality-oriented, scientific and technological innovation, scientific management, excellent products, and a good reputation—we wholeheartedly provide customers with the most satisfactory service.
Human Resources
Our existing engineering and technical staff account for 55% of our workforce. The professional management team, assisted by the company's ERP system, serves customers scientifically and efficiently in accordance with the ISO9001 system.
Our Team
We have more than 10 technical engineers, 6 drawing engineers, 8 quality inspection engineers, and 12 professional domestic and foreign sales engineers.
Our Markets
Our products are sold both domestically and internationally, particularly in North America and Europe. For example, we have customers in the United States, Canada, Germany, Switzerland, France, Italy, the Netherlands, Belgium, Poland, Spain, Ukraine, and more.
Types of Powder Metallurgy
Pressing and sintering
This is the most common method of producing PM parts. In this process, the powder is first compacted into the desired shape under high pressure and then sintered at high temperatures to fuse the particles together. The resulting component is porous and can be further machined to achieve the desired final dimensions.
Metal injection molding (MIM)
Metal injection molding is a process that combines the techniques of powder metallurgy and plastic injection molding. The process begins with the production of a feedstock material, which is a mixture of metal powder and a binding agent. The feedstock is then heated and injected into a mold cavity under high pressure. After cooling, the part is debound and sintered to remove the binding agent and achieve high density.
Hot isostatic pressing (HIP)
This process involves the application of hydrostatic pressure and high temperature to consolidate the powder into a dense material. The powder is placed into a flexible mold, which is then subjected to high pressure and temperature. The resulting product is fully dense and free of any porosity.
Cold isostatic pressing (CIP)
In this process, the powder is placed into a flexible mold and subjected to high pressure and room temperature. The resulting product is then sintered to achieve the desired density and strength.
Spark plasma sintering (SPS)
This process is a relatively new technique that uses an electric current to heat the powder to high temperatures and apply pressure simultaneously. The process produces parts with very high density and excellent mechanical properties.
Additive manufacturing (AM)
Additive Manufacturing, also known as 3D printing, is a technique used to produce parts by adding layers of material one on top of the other. In the PM industry, this process is often used to produce parts with complex geometries and small features that are difficult or impossible to produce through conventional PM techniques.
Application of Powder Metallurgy
Automotive industry
Powder metallurgy has extensive applications in the automotive industry, especially for the production of engine components such as gears, bearings, bearings, and bushings. Powder metallurgy offers high strength, durability, and wear resistance, which is essential for automotive components.
Aerospace industry
The aerospace industry is another field where powder metallurgy has significant applications. The method is used to produce various critical components such as turbine blades, impellers, and combustion chambers that demand the highest quality and reliability.
Medical industry
Powder metallurgy is also an essential process for the medical industry. It is utilized to produce orthopedic implants, dental implants, and prosthetic devices. Powder metallurgy offers excellent biocompatibility, corrosion resistance, and mechanical properties.
Electrical & electronics industry
The electrical and electronic sectors are two areas where powder metallurgy finds extensive applications. It is useful for manufacturing a broad range of components such as magnetic materials, sensors, and capacitors
Defense industry
The defense sector is yet another field where powder metallurgy is of significant importance. Components such as armor plate, gun barrels, and missile casings rely on the uniformity and high strength of the powder metallurgy process.
Mining industry
Powder metallurgy finds extensive application in the mining industry for producing hard-wearing components such as drilling bits, cutting teeth, and wear plates.
Powder production
The first step in the process of powder metallurgy involves creating the finely powdered materials that will be used to form the final product. This can be done using several different methods, including atomization, chemical reduction, and mechanical alloying. In atomization, molten metal is sprayed into a fine mist, which cools and solidifies to form tiny, uniform particles. In chemical reduction, metal oxides are reduced to their pure metal form using a reducing agent. In mechanical alloying, powders of different metals are mixed together in a ball mill, resulting in a homogeneous mixture that can be used to create alloys.
Powder blending
Once the powders have been produced, they are blended together to create a uniform mixture that will produce the desired alloy or composition. This step is important because it ensures that the final product will have the desired properties and characteristics.
Compaction
The blended powders are then compressed into a desired shape using a press. This process is called compaction. During compaction, the powders are typically pressed into a die cavity using a hydraulic press, resulting in a compact that is roughly the size and shape of the final product.
Sintering
After compaction, the compacted powders are heated in a furnace at high temperatures. This process is called sintering. During sintering, the powders are heated to a temperature just below their melting point, causing them to fuse together. The result is a solid material with a very high density and strength.
Finishing
Once the sintering process is complete, the final product may be subjected to additional finishing steps to achieve the desired surface finish, dimensional accuracy, and other properties. This may include machining, grinding, polishing, or other techniques.
Components of Powder Metallurgy
Metal powders
Metal powders are the primary starting materials for powder metallurgy. They are produced by a variety of methods such as atomization, chemical reduction, or mechanical grinding. The powders are available in various grades and sizes depending on the specific application.
Mixing and blending
The metal powders are carefully blended to form a homogenous mixture. The blending process ensures that the different powders are evenly distributed in the mixture, which is essential for obtaining consistent properties.
Compaction
Compaction is used to transform the blended powder into a desired shape or form. The compacted material is often referred to as a "green compact" and is highly porous.
Sintering
Sintering is a high-temperature process that involves heating the green compact to a temperature just below the melting point of the metal. The process promotes a solid-state diffusion of the metal particles, leading to the formation of strong bonding between the particles. Sintering reduces the porosity of the green compact, increases its density, and improves its mechanical properties.
Machining and finishing
Machining and finishing are the final steps in powder metallurgy. The sintered part is machined to the required final dimensions, followed by a surface finishing process to achieve the desired surface finish and appearance.
Powder metallurgy is a form of material processing that utilizes the compacted powders of metallic and non-metallic substances. It is a technique that enables the creation of parts and components that are of high accuracy, strength, and density, as well as having an excellent surface finish with varied options for materials and attributes.The process of powder metallurgy begins with the selection of the material to be used, which can be a combination of elements such as iron, copper, nickel, aluminum, tungsten, etc. The material is then processed and refined to the desired particle size and shape, which is critical for optimal compaction.
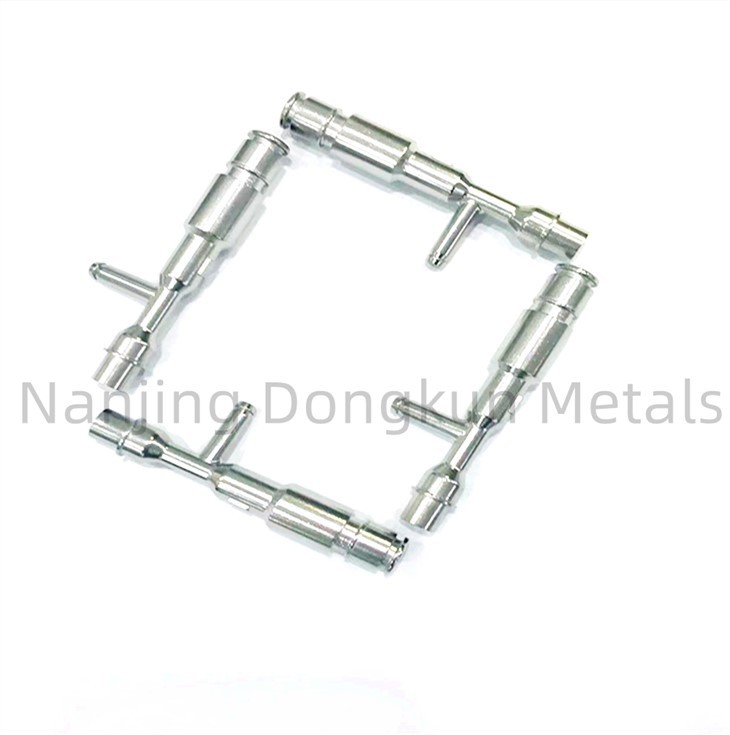
How to Maintain Powder Metallurgy
Inspect the process regularly
Regular inspection is crucial for ensuring the quality of the Powder Metallurgy process. It helps to identify potential defects, such as cracks, voids, and surface roughness in the finished product. Inspections should be carried out at various stages of the manufacturing process, including powder blending, compaction, sintering, and post-treatment.
Control the environment
PM requires a controlled environment to ensure consistent quality and minimize defects. The temperature, humidity, and air quality must be monitored and controlled to prevent oxidation and contamination. The equipment and tools must be cleaned and maintained regularly to prevent contamination.
Monitor the equipment
The equipment used in the PM process must be regularly checked and maintained to ensure that they are functioning correctly. This includes the press, molds, sintering oven, and other tools. Regular maintenance helps to prevent equipment failure and costly downtime.
Properly store the powders
Metal powders used in the Powder Metallurgy process are sensitive to environmental conditions and must be stored in a dry and clean place to prevent contamination. The powders should also be stored in appropriate containers that prevent exposure to moisture, air, and other contaminants.
Follow proper mixing procedures
The quality of the PM product depends heavily on the proper mixing of the metal powders. Incorrect mixing can lead to non-uniform distribution of the powders, resulting in defects in the finished product. Therefore, it is essential to follow proper mixing procedures and use the correct amount of materials.
Ensure proper compaction
Proper compaction of the metal powders is necessary to create a strong, dense, and uniform product. Too much or too little compaction can result in defects in the product, such as cracks, warping or distortion. Therefore, it is essential to follow proper compaction procedures and use appropriate pressure and tooling.
Optimize the sintering process
Sintering is the process of heating the compacted metal powder to a temperature below its melting point. The process helps to fuse the powder particles together, forming a solid and dense component. Optimizing the sintering process involves controlling the temperature, time, and atmosphere to achieve the desired density and strength of the finished product. Regular monitoring of the sintering process is necessary to identify any deviations and make necessary adjustments.
Ferrous materials
Powder metallurgy can be used to produce ferrous materials such as iron, steel, and stainless steel. These materials have good strength, wear resistance, and corrosion resistance.
Non-ferrous materials
Powder metallurgy can also be used to produce non-ferrous materials like copper, aluminum, titanium, and nickel, which have high strength, good conductivity, and excellent surface finish.
Hard materials
Powder metallurgy can be used to produce hard materials like tungsten carbide, cobalt, and diamond, which have excellent wear resistance, hardness, and toughness.
Magnetic materials
Powder metallurgy can be used to produce magnetic materials like iron, cobalt, and nickel alloys, which are used in motors, generators, and transformers.
Self-lubricating materials
Powder metallurgy can be used to produce self-lubricating materials like bronze, which can reduce friction and wear in machinery and equipment.
Biomedical materials
Powder metallurgy can be used to produce biomedical materials like titanium alloys, which are used in orthopedic implants and dental implants due to their biocompatibility and corrosion resistance.
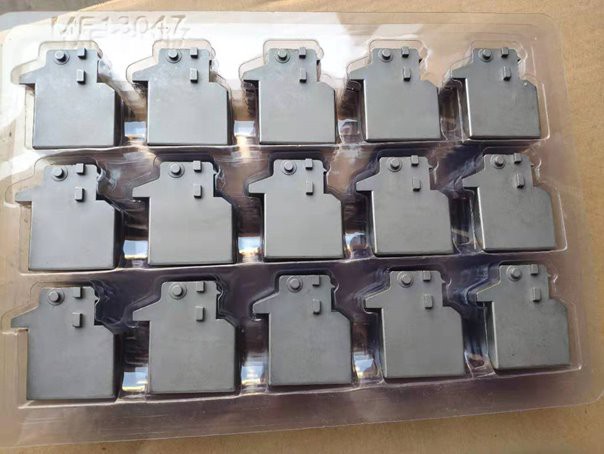
The powder metallurgy process starts with the production of metal powders which can be obtained through a variety of methods such as atomization, chemical reduction, and mechanical milling. The resulting powder is then screened to remove contaminants and achieve the desired size distribution.Once the metal powder has been obtained and processed, it is ready to be formed into a component. The first step in this process is known as compaction, which involves pouring the metal powder into a die and pressing it under high pressure to form a compact mass. Various methods of compaction can be used such as cold pressing, hot pressing or isostatic pressing.After the compacting stage, the green component is then sintered, which is where the metal particles are bonded together by heat and pressure. During sintering, the metal powder is heated to a temperature just below its melting point to allow for the individual particles to bond together and form a solid component.Finally, the sintered component is then subjected to various finishing operations such as machining, grinding, and polishing to achieve the desired final shape, surface finish, and dimensional accuracy.
How Does the Sintering Process Affect the Properties of the Final Product
Sintering is a process used in the manufacturing of various materials including ceramics, metals, and plastics. The process involves heating a powdered material until the particles fuse together to form a solid mass. Sintering is an important stage in the production process as it has a significant impact on the properties of the final product.One of the major effects of sintering is on the density of the material. As the material is heated, the particles start to pack more closely together, resulting in an increase in density. This increased density can lead to improved mechanical properties, such as increased strength and hardness, as well as improved electrical conductivity.Sintering also has an impact on the microstructure of the material. During the process, the individual particles start to bond together, forming a homogenous structure. This can lead to improved uniformity in the material, which can improve its corrosion resistance and overall durability.
What Are the Different Processes and Methods of Powder Metallurgy
Powder production
The first step in powder metallurgy is the production of metal powder. There are many methods of powder production, including atomization, mechanical grinding, chemical reduction and electrolysis. Each method has its own advantages and is chosen based on the desired powder characteristics.
Powder blending
Once metal powders are produced, they are often blended with other powders or additives to achieve the desired properties. This mixing process may involve mixing different metal powders, adding lubricants or binders, or incorporating alloying elements.
Pressing
During the pressing process, the mixed powder is placed into a mold and high pressure is applied to form a compact. Pressure helps consolidate the powder and form a solid shape. Compaction can be carried out using various techniques, such as uniaxial pressing, isostatic pressing or cold isostatic pressing.
Sintering
Sintering is a critical step in powder metallurgy. The compacted parts are heated in a controlled atmosphere to a temperature below the melting point of the metal. During the sintering process, the metal particles bond together to form a strong, dense part. The sintering process helps eliminate porosity, increases strength and improves dimensional stability.
Secondary operations
After sintering, additional secondary operations can be performed to further enhance the performance of the part. These operations can include heat treatment, machining, surface finishing and coating. Heat treatment improves mechanical properties, while machining and finishing operations help achieve the desired shape and surface quality.
Penetration
In some cases, sintered parts may undergo a penetration process. Penetration involves impregnating parts with a low melting point metal or alloy. This helps fill in any remaining voids and increases the density and strength of the part.
Hot isostatic pressing (HIP)
Hot isostatic pressing is a post-sinter process used to further densify the part and eliminate any remaining porosity. Sintered parts are subjected to high temperatures and pressures in an inert gas environment. HIP improves mechanical properties and enhances part integrity.
Additive manufacturing
Additive manufacturing, also known as 3D printing, is a relatively new method in powder metallurgy. It involves depositing metal powder layer by layer using various techniques, such as selective laser sintering (SLS) or electron beam melting (EBM). Additive manufacturing can produce complex and customized metal parts with high precision.
Training
Operators of powder metallurgy equipment should be properly trained on the safe and correct operation of the equipment. This training should include instruction on the proper use of personal protective equipment, the safe handling of powder metallurgy materials, and the correct procedures for starting and stopping the equipment.
Workplace safety
The workplace should be free of any hazards that could pose a risk to workers. This includes ensuring that the area is well-lit and free of trip hazards, and that all equipment is properly maintained and in good working order.
Material handling
Powder metallurgy materials can be dangerous if not handled properly. Workers should be trained on the safe handling of these materials, including how to properly store and handle them, and how to avoid exposure to dust and fumes.
Machine maintenance
Regular maintenance and inspection of the powder metallurgy equipment is essential to ensure safe and efficient operation. This includes checking the condition of the machine's moving parts, hydraulic systems, and electrical components, and ensuring that all safety devices and interlocks are functioning properly.
Emergency preparedness
In the event of an emergency, it's important to have a plan in place to ensure the safety of workers and the environment. This plan should include procedures for shutting down the equipment, evacuating the workplace, and dealing with any potential hazards.
Compliance with regulations
Operators of powder metallurgy equipment should be aware of and comply with all applicable regulations and standards, including those related to workplace safety, environmental protection, and product quality.