What Is CNC Machining?
CNC machining refers to the process of using computer numerical control (CNC) machines to manufacture a wide range of parts and products from various materials. These machines use programmed instructions to control their movements and operations, enabling precise and accurate production of complex shapes and intricate designs.CNC machines are commonly used in the manufacturing industry for applications such as milling, turning, drilling, and cutting. They can work with a variety of materials, including metals, plastics, composites, and wood, and can produce parts in small or large volumes with consistent quality and accuracy.
Advantages of CNC Machining
Precision
CNC machines are capable of producing parts with high levels of accuracy and consistency. This is particularly important for industries where precision is paramount, such as aerospace, medical, and defense.
Efficiency
CNC machines can work 24 hours a day, seven days a week, and are capable of producing large quantities of parts in a short amount of time. This can help manufacturers meet tight deadlines and reduce production costs.
Flexibility
CNC machines are highly flexible and can be easily reprogrammed to produce different parts and products. This allows manufacturers to quickly adapt to changes in market demands and production requirements.
Reduced waste
CNC machines are designed to operate with minimal waste, as they are programmed to maximize material usage and minimize scrap. This can help manufacturers lower their production costs and reduce their impact on the environment.
Improved safety
CNC machines are fully automated and do not require operators to be in close proximity to the cutting tools. This helps to reduce the risk of workplace injuries and makes CNC machining a safer option for workers.
Complexity
CNC machines are able to machine extremely complex parts with precise dimensions that may not be possible with traditional manufacturing methods. This allows manufacturers to create custom-made parts for specific applications.
-
1333333333
33333333333333333333333333333333333333333333333333333333333333333333333333333333333333333333333333333333333333333333333333333333333333333333333333333333333333333333333333333333333333333333333333333333 -
111
11
Why Choose Us
Corporate Culture
Quality-oriented, scientific and technological innovation, scientific management, excellent products, and a good reputation—we wholeheartedly provide customers with the most satisfactory service.
Human Resources
Our existing engineering and technical staff account for 55% of our workforce. The professional management team, assisted by the company's ERP system, serves customers scientifically and efficiently in accordance with the ISO9001 system.
Our Team
We have more than 10 technical engineers, 6 drawing engineers, 8 quality inspection engineers, and 12 professional domestic and foreign sales engineers.
Our Markets
Our products are sold both domestically and internationally, particularly in North America and Europe. For example, we have customers in the United States, Canada, Germany, Switzerland, France, Italy, the Netherlands, Belgium, Poland, Spain, Ukraine, and more.
Types of CNC Machining
Milling
CNC milling is the most common type of CNC machining process. Milling involves the use of a rotating cutting tool to remove material from a workpiece. The milling machine uses various tools, including end mills, ball mills, and facemills, which are controlled by the CNC program. Milling can be used to create complex shapes, holes, and channels. It is ideal for creating parts that require tight tolerances, such as aerospace components.
Turning
CNC turning is another essential type of CNC machining. Turning involves rotating a workpiece while a cutting tool removes material to create a symmetrical shape. During this process, the tool moves along the length of the workpiece, creating components such as shafts, cylinders, and cones. Turning is the ideal process for creating parts with a cylindrical or conical shape.
Drilling
CNC drilling is similar to milling, but it involves drilling holes in a workpiece. CNC drilling machines can work at high speeds and produce holes of varying sizes and shapes. It is ideal for creating precise holes in parts such as printed circuit boards, engine blocks, and gears.
Grinding
CNC grinding is a precision machining process that removes material from a workpiece using a rotating abrasive wheel. It is used to create high-precision parts with a fine surface finish. CNC grinding is commonly used in the aerospace, medical, and automotive industries.
Electrical discharge machining (EDM)
EDM is a non-traditional machining process that uses electrical discharges to shape a workpiece. EDM machines can create precise features in metal, plastic, and other materials that are challenging to machine using traditional methods. The process also offers the ability to create complex shapes with a high degree of accuracy.
Laser cutting
CNC laser cutting is a process that utilizes a high-power laser to cut through a workpiece. Laser cutting is a fast and precise method of cutting materials such as metal, plastic, and wood. It is ideal for creating parts with intricate shapes, such as gears.
Application of CNC Machining
Aerospace industry
CNC machining is an essential component of modern aerospace manufacturing. It is used to manufacture complex and precision parts for aircraft engines, landing gear, and other aircraft components. The high accuracy and reliability of CNC machines make them ideal for producing aerospace components that require rigorous performance standards.
Automotive industry
CNC machining plays a crucial role in the automotive industry by producing components such as engine blocks, gearboxes, brake components, and suspension systems. CNC machines can produce parts with a high degree of accuracy and consistency, ensuring that all components fit together perfectly and function as intended.
Medical industry
CNC machining is used in the medical industry to produce precision medical devices and implants. CNC machines can create complex shapes and designs that would be difficult to manufacture using traditional methods. This technology is used to manufacture orthopedic implants, dental implants, and other medical devices.
Defense industry
CNC machining is used in the defense industry to manufacture components such as gun barrels, missile casings, and other military hardware. CNC machines can produce parts with a high level of accuracy and consistency, which is essential for maintaining safety and reliability in military equipment.
Electronics industry
CNC machining is used to produce computer and electronic components such as printed circuit boards, computer housings, and other electronic parts. The precision and efficiency of CNC machines make them ideal for producing components that require intricate designs and high tolerances.
Manufacturing industry
CNC machining is widely used in the manufacturing industry to produce various parts and components for different products. It is employed in the production of consumer goods, industrial machinery, and other products, where precision and repeatability are crucial.
CNC machining is a popular manufacturing process that combines two techniques - casting and CNC (Computerized Numerical Control) machining - to produce precision parts with complex geometries. It involves melting a metal or alloy and pouring it into a mold to create a casting. Then, the casting is machined to achieve the desired shape and finish using CNC machines.The maximum size of parts that can be produced through casting CNC machining depends on several factors, including the type of material being used, the size of the casting equipment, and the capabilities of the CNC machines. In general, casting CNC machining can produce parts ranging from small to large sizes, with some manufacturers capable of producing castings up to several meters in length and weighing several tons.
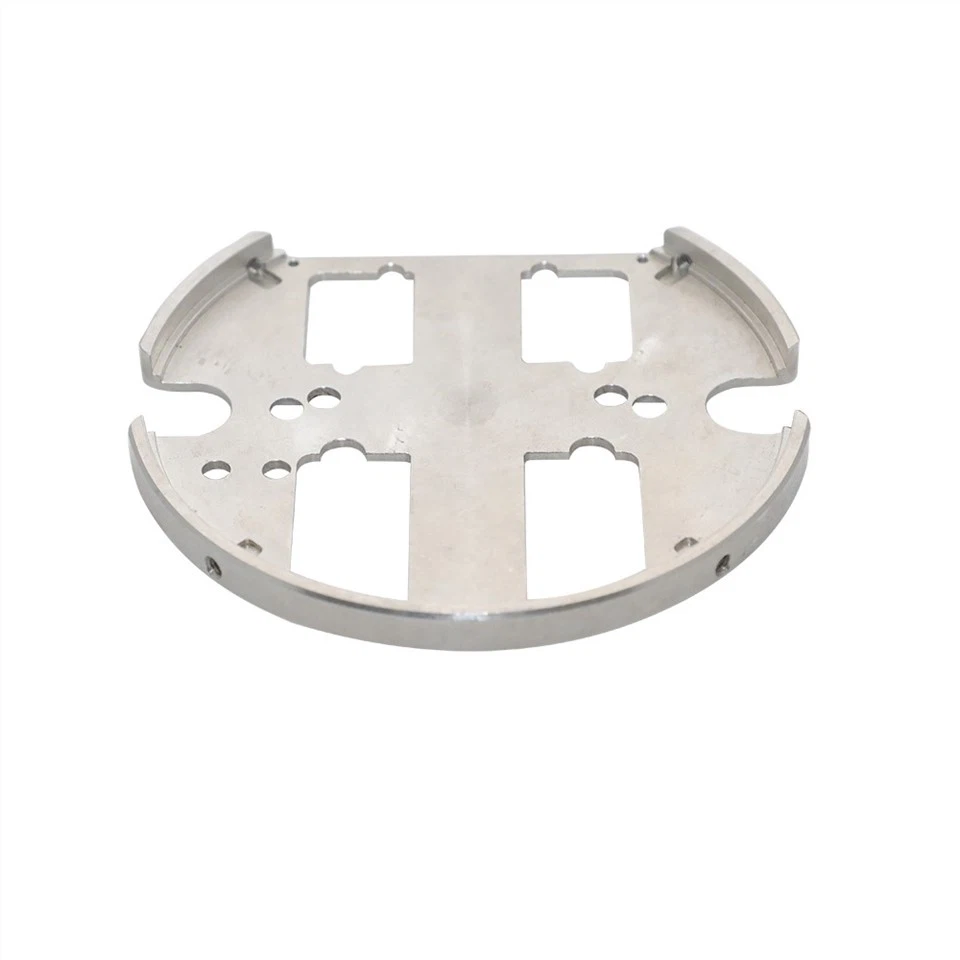
Process of CNC Machining
Design of the part
The first step in the casting CNC machining process is to design the part that needs to be produced. This can be done using computer-aided design (CAD) software.
Creation of the mold
Once the part has been designed, a mold must be created. The mold is typically made of a material like plaster or silicone rubber. The mold is created by pouring the material into a mold box, which is then left to dry overnight.
Casting
After the mold has dried, it is ready for casting. The material used to cast the part depends on the requirements of the part. Common materials include aluminum, brass, and steel. The material is melted in a furnace and then poured into the mold. The molten metal is allowed to cool and solidify into the pre-formed shape of the part.
Removal from mold
After the metal has cooled and solidified, the part is removed from the mold. This is typically done by breaking the mold or using a release agent on the mold surface.
Rough machining
The next step in the process is rough machining. In this process, excess metal is removed from the pre-formed shape of the part. This is done using a variety of tools and techniques, such as milling or drilling.
Final machining
After rough machining, the part is finished using CNC machining. This step involves the use of computer-controlled machinery to cut, grind, or polish the part to final dimensions and tolerances.
Inspection
After the part has been finished, it is inspected to ensure that it meets the required specifications. This step is important to ensure that the finished part meets the required quality standards.
Finishing
The last step in the process is finishing. This involves applying any necessary surface coatings or treatments to the part, such as painting or anodizing.
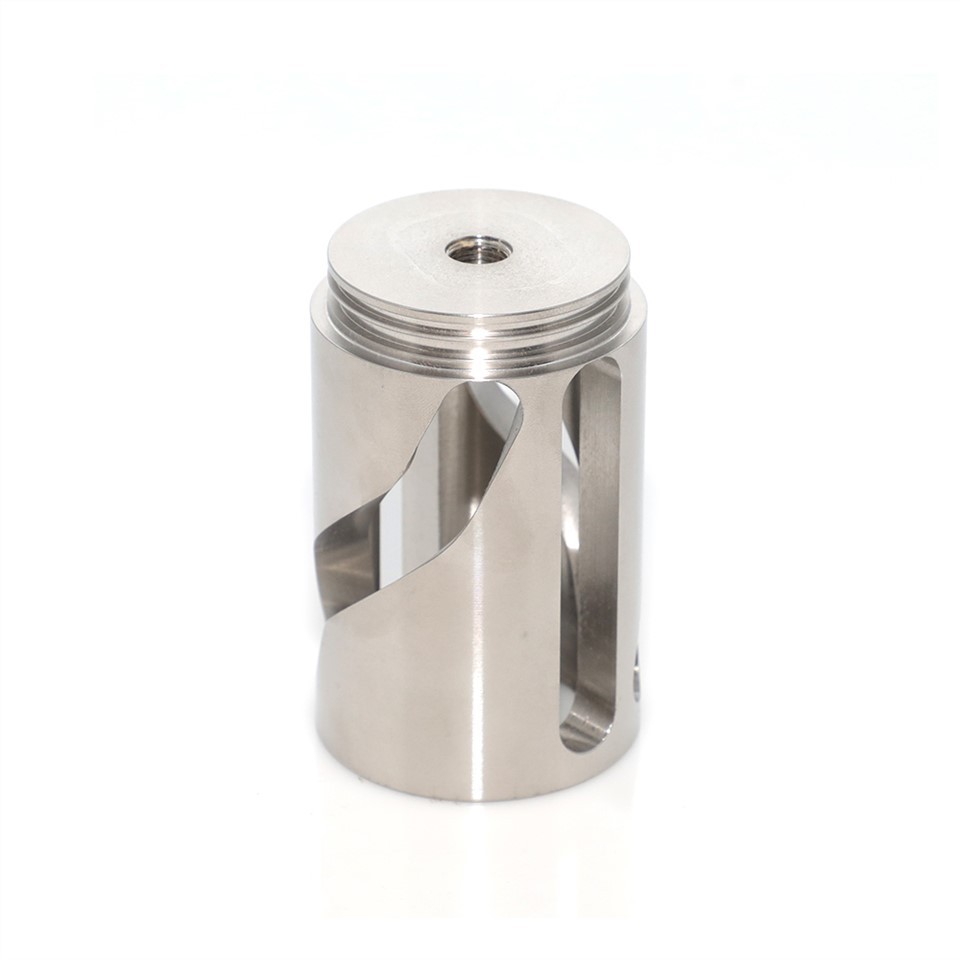
The primary difference between casting CNC machining and traditional machining is the process of casting. Traditional machining typically starts with a solid block of material that is then shaped and refined using a variety of cutting tools. This process is known as subtractive manufacturing since material is removed from the raw block to create a finished product. In contrast, casting involves pouring molten material into a mold, allowing it to cool and solidify, and then removing the finished part from the mold. This process is known as additive manufacturing since the part is created by adding material to the mold rather than by removing material from a block.
What Materials Can Be Used for CNC Machining of Castings
Aluminum
Aluminum is a lightweight and durable metal widely used in manufacturing. It is easy to process and is known for its excellent corrosion resistance, making it suitable for a wide range of applications.
Stainless steel
Stainless steel is a strong, durable, and corrosion-resistant material used in a variety of applications, including marine, aerospace, and medical applications. It is also an excellent thermal conductor, making it suitable for applications requiring high temperature resistance.
Titanium
The versatility of titanium makes it an ideal metal for a variety of applications, including sports equipment, eyeglasses frames, watches, and jewelry. Its strength and durability make it a popular choice for outdoor gear, such as camping and hiking equipment.
Zinc
Zinc is a versatile and low-cost material that is often used to cast small and complex parts. It is easy to machine and its excellent casting properties make it suitable for producing complex geometries.
Brass
Brass is an alloy of copper and zinc that has good mechanical properties and is suitable for producing complex parts with excellent durability. It is also corrosion-resistant and has excellent thermal conductivity.
Copper
Copper has become a common material for casting CNC machining due to its excellent electrical and thermal conductivity. It is commonly used in the manufacture of electrical components, sink fittings and heat exchangers.
CNC machining is highly precise and accurate. It offers a level of accuracy that is not possible with manual machining processes. With CNC machining, the level of accuracy that can be achieved depends on various factors, including the type of machine, the cutting tools being used, and the complexity of the design.Modern CNC machines are equipped with advanced tools and control systems that allow them to achieve very high levels of precision. For example, a typical CNC lathe can achieve a positioning accuracy of ±0.0002 inches, and a repeatability accuracy of ±0.0001 inches. A CNC milling machine, on the other hand, can achieve a positioning accuracy of ±0.0005 inches, and a repeatability accuracy of ±0.0002 inches.In addition to the type of machine and tools used, the accuracy of CNC machining also depends on the complexity of the design being produced. Designs that have simple geometries and features can generally be machined with a high degree of accuracy. However, more complex designs may require additional setup and tool changes to achieve the required level of precision.
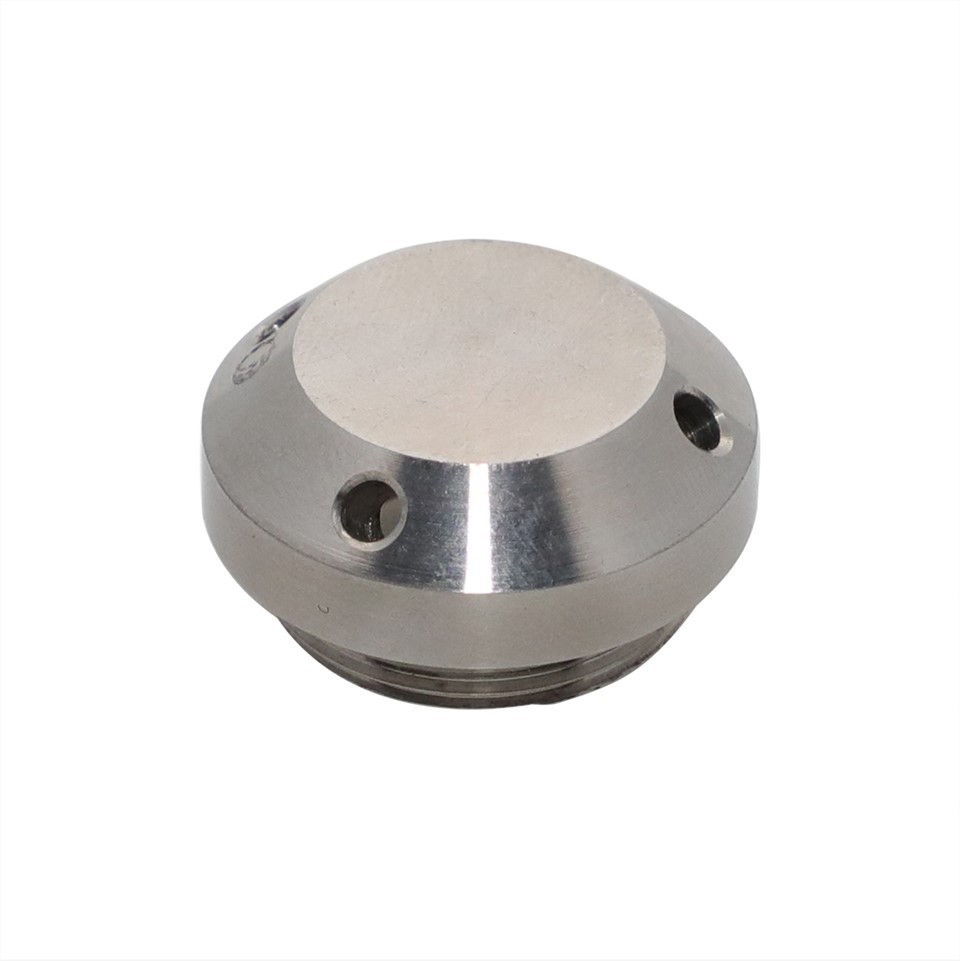
What Post-Processing Options Are Available for Parts Produced by CNC Machining
Deburring
This process removes any rough edges or burrs left on the parts during machining. Deburring is typically performed using abrasive blasting, grinding, or tumbling.
Tumbling
This process is used to enhance the surface finish of parts produced by CNC machining. Tumbling involves placing the parts in a rotating drum along with abrasive media such as sand or ceramic beads.
Anodizing
This process is used to add a protective coating to the surface of the aluminum parts. Anodizing can also improve the appearance of the parts by adding color or a sheen to the surface.
Powder coating
This process involves spraying a dry powder onto the surface of the part and curing it in an oven. Powder coating creates a durable and protective layer that also improves the appearance of the part.
Heat treating
This process is used to improve the strength, hardness, and durability of parts produced by CNC machining. Heat treating involves heating the part to a specific temperature and then cooling it down slowly.
Electroplating
This process involves depositing a thin layer of metal onto the surface of the part through an electrochemical process. Electroplating can improve the appearance of the part and protect it from corrosion.
Laser marking
This process involves using a laser to etch a permanent mark onto the surface of the part. Laser marking can be used to add logos, serial numbers, or other identifying information to the part.
How to Maintain CNC Machining
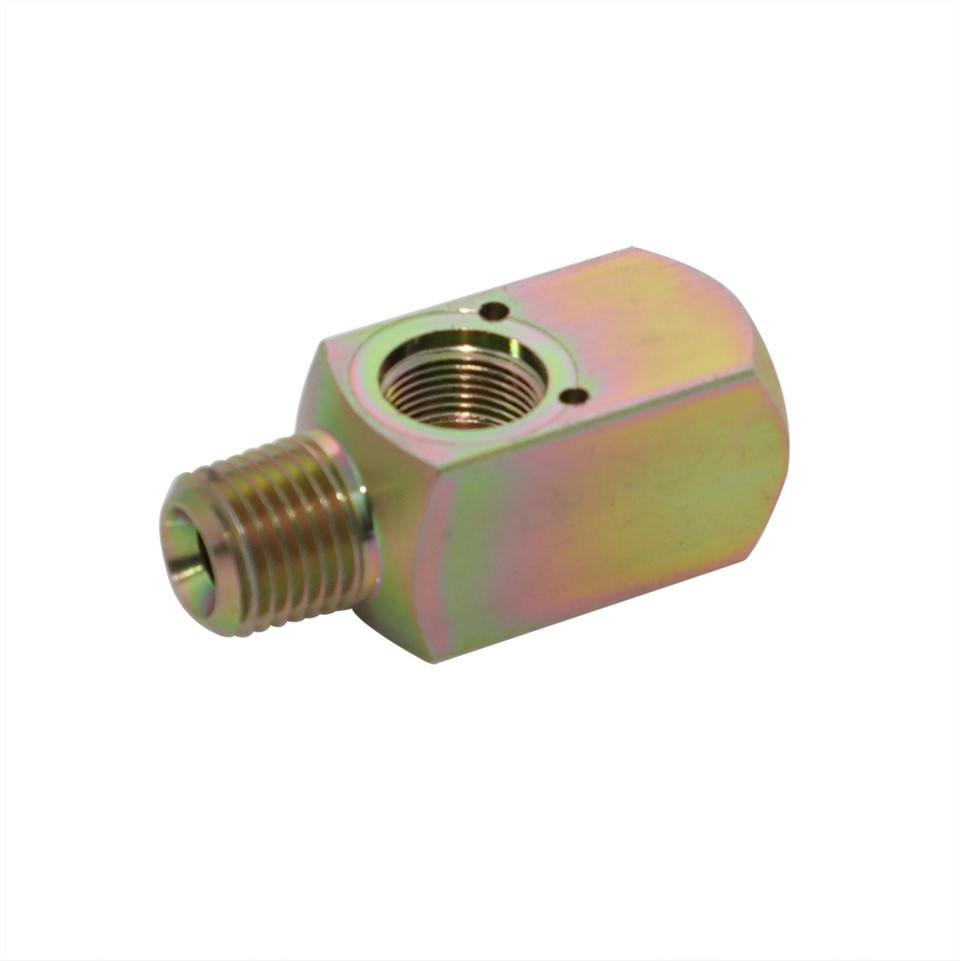
01.Keep the machine clean
02.Lubricate regularly
03.Check and replace worn out parts
04.Update software and firmware
05.Calibrate the machine
06.Train operators
Material of CNC Machining
Metal
Metals are a popular choice for CNC machining due to their strength and durability. Common metal materials include steel, aluminum, titanium, and copper.
Plastic
Plastics are another popular choice for CNC machining due to their versatility and cost-effectiveness. Common plastic materials include ABS, PC, and PVC.
Wood
Wood is a natural material that can be easily machined using CNC machines. It is commonly used for prototyping and low-volume production runs.
Composite materials
Composite materials are a combination of two or more materials that are combined to create a new material with unique properties. Common composite materials include carbon fiber, glass fiber, and Kevlar.
Ceramic
Ceramics are a popular choice for CNC machining due to their high melting point and toughness. Common ceramic materials include porcelain and stoneware.
Other materials
Other materials that can be machined using CNC machines include stone, glass, and stoneware. The choice of material will depend on the specific requirements of the project.
Components of CNC Machining
CNC machine
The CNC machine is the main component of the CNC machining system. It is a computer-controlled machine tool that can perform various machining operations, such as milling, turning, drilling, and grinding. The machine consists of a base, worktable, spindle, tooling, and controls.
Computer-aided design (CAD) software
CAD software is used to create a digital model or design of the part to be machined. The software allows for precise and detailed design, including dimensions, geometries, and tolerances. The CAD file is then used to generate the CNC program.
Computer-aided manufacturing (CAM) software
CAM software is used to convert the CAD design into a CNC program or code. The software generates the toolpaths and instructions that the CNC machine will follow to machine the part. CAM software takes into account factors such as tool selection, cutting speeds, feeds, and machining strategies.
CNC controller
The CNC controller is the brain of the CNC machine. It receives the CNC program and translates it into electrical signals that control the movement and operation of the machine. The controller controls the axes (X, Y, Z) of the machine, spindle speed, tool changes, coolant flow, and other machine functions.
Servo motors
Servo motors are used to drive the axes of the CNC machine. They receive signals from the CNC controller and move the machine's components, such as the worktable, spindle, and tool, with high precision and accuracy. Servo motors provide smooth and controlled movement.
Tooling
Tooling refers to the cutting tools used in CNC machining. These include end mills, drills, taps, reamers, and inserts. The selection of the appropriate tooling depends on the material being machined, the desired operation, and the geometry of the part.
Workholding devices
Workholding devices are used to secure the workpiece in place during machining. These can include vises, clamps, chucks, fixtures, and collets. Workholding devices ensure that the workpiece remains stable and properly positioned during machining operations.
Coolant system
A coolant system is used to cool and lubricate the cutting tools and workpiece during machining. Coolant helps to dissipate heat, reduce friction, and remove chips and debris from the cutting zone. Common coolants include water-soluble oils, synthetic fluids, and compressed air.
Measurement and inspection tools
Measurement and inspection tools, such as calipers, micrometers, gauges, and coordinate measuring machines (CMM), are used to verify the accuracy and quality of machined parts. These tools ensure that the dimensions and tolerances of the part meet the required specifications.
FAQ